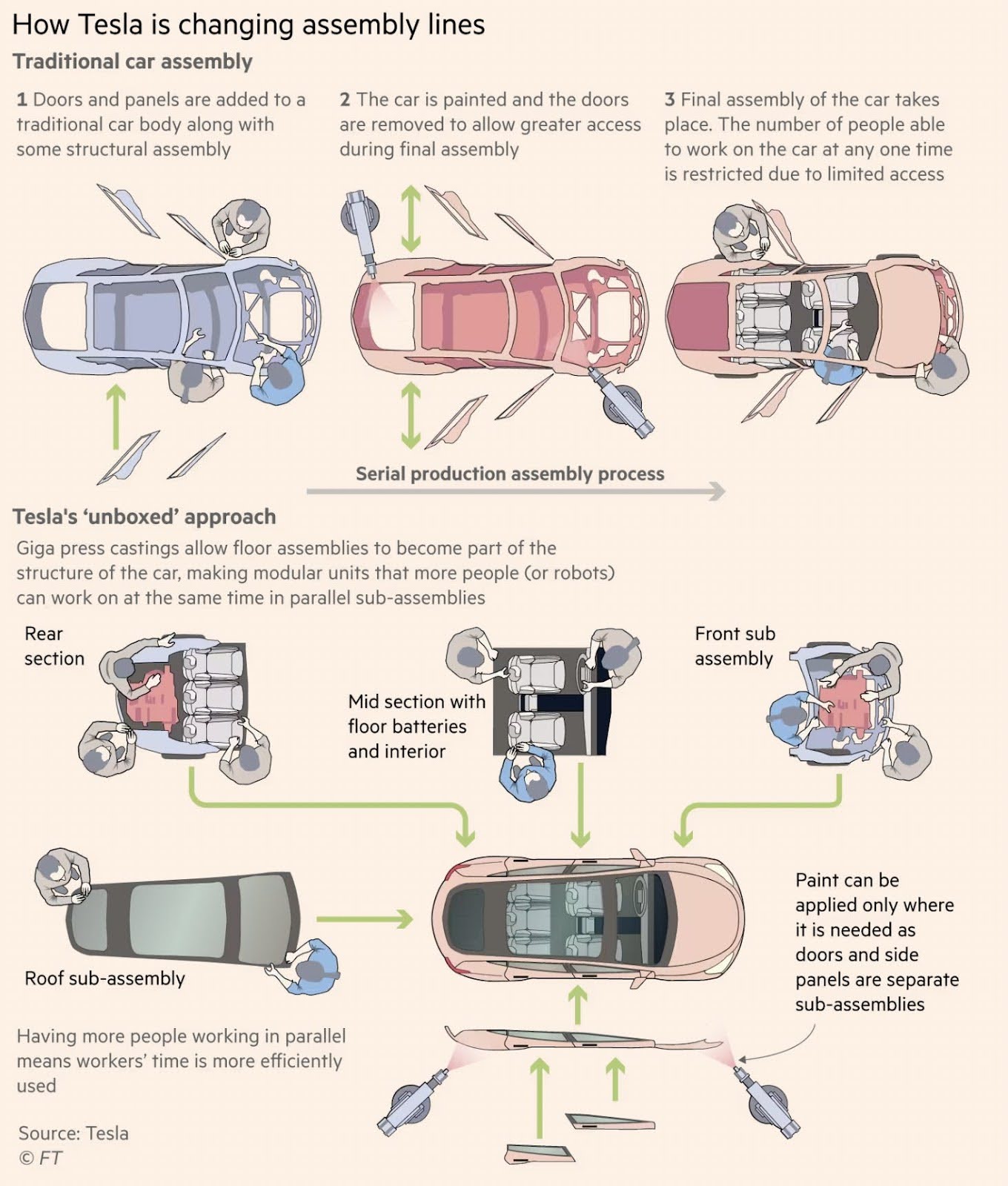
Illustrations showing difference between traditional assembly lines and Tesla "unboxed" approach.
Image Description
The image illustrates the difference between traditional car assembly lines and Tesla's "unboxed" approach. The traditional method shows a sequential process, while Tesla's method highlights parallel sub-assemblies with modular units, allowing more simultaneous work.
Positive Aspects
The image effectively contrasts two different assembly line strategies. It visually simplifies complex processes, making it easy to understand the efficiency gains Tesla is achieving with its innovative approach. The use of arrows and labeled sections guides the viewer through the process clearly.
Key Takeaways
- Traditional Assembly: Sequential and restricted access limits the number of workers who can contribute simultaneously.
- Tesla's 'Unboxed' Approach: Uses Giga press castings to create modular sub-assemblies that allow for parallel work, enhancing efficiency.
- Efficiency Gains: More parts are worked on at the same time, optimizing workers' time and reducing bottlenecks.
- Targeted Painting: Paint is applied only where needed, which reduces waste and time.
- Robotic Integration: The approach allows more robots to work in parallel, increasing automation and precision.
Additional Insights
Tesla's innovation in assembly lines is akin to breaking a huge jigsaw puzzle into smaller, manageable pieces that can be worked on simultaneously. This not only speeds up production but also allows for more flexibility and adaptability in the manufacturing process. Imagine a kitchen where every chef can have their own station and all ingredients are prepped simultaneously, rather than waiting for one person to finish before the next starts. This is the culinary equivalent of Tesla's "unboxed" strategy!